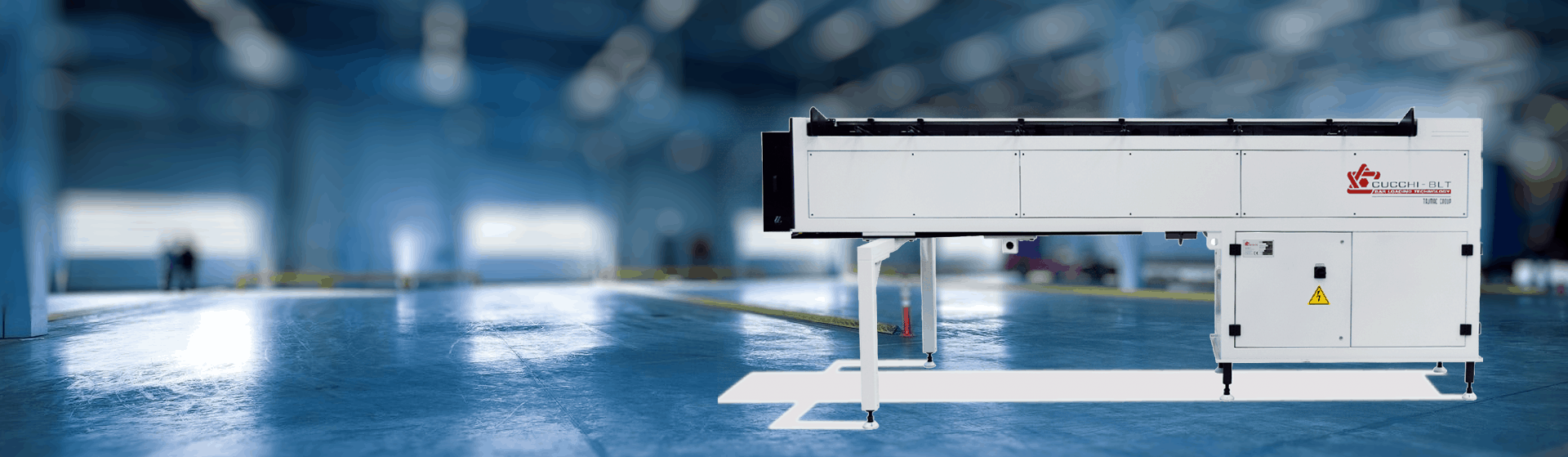
Cucchi-BLT 6 or 8 Multi Spindle Bar Loaders
About The Cucchi Bar Loaders
CUCCHI BLT bar loader models MULTI and MULTls are available for all types of machinery and all manufactured multispindles. The bar loader is interfaced to the lathe by means of a coupling that transfers the indexing movement from the lathe. The coupling is designed specifically for each individual lathe specification and model. The custom tailoring guarantees the quality of the mechanical and electrical interface.
Improve Your Productivity
Features & Benefits
Features
- Bar length: 3.20m-3.3 0m-3.70m-4.00m-4. 30m-4.50m (For different lengths please contact the manufacturer)
- Bar straightness: The prescribed straightness deviation of the bars to be worked should be max 0.5 mm/m.
- Lubricating oil: Hydraulic 46
- Operating air pressure: Minimum 6 bar
- Voltage: 23 0/400V
- Feeding speed: Max. 1000 mm/sec
- Min. bar changing time: 20sec.
- Magazine Capacity: From 600 mm to 1000 mm width.
- The use of feeding systems that employ hydraulic motors
- Removal of the feed fingers and consequent increase in the machining capacity of the lathe.
- Loading operation partially in masked time, in accordance with the lathe.
- The use of die-cast synthetic resin conceived to dampen vibrations and reduce the noise generated by the rotating bars;
- Possibility to run bars of any shape and material: round, hexagonal and square.
- Rear extraction of the bar remnant.
Benefits
The stock tube elements of the bar-guide drum are realised in die-cast synthetic resin, a self-lubricating, elastic material conceived to dampen vibrations. The guide seat is completed with a hardened-steel insert.
This device is positioned on bearings at the lathe spindle entrance in the area where the loader guides do not support the bar. The device prevents problems of instability and vibration of bars.
The centering of the bar, of any shape (round, hexagonal and square), is ensured by the twisting of the rods on the bar itself, with an automatic release at the point when the pusher passes through.
This device is applied directly to the rear lathe spindle. The bushing has a relief feature which allows it to receive the maximum diameter of the pusher. At the front there is a quick release insert with a nominal diameter equal to the worked bar.
The spring bushing guides the pusher and the bar for the entire length of the spindle to the lathe collet, improving the centering action. The connection and release of the spring bushing is automated.
This device is positioned in the loader guide channels and reduces the swinging of the bars in the channel itself.
The centering forks are constructed from plastic materials and are positioned at regular intervals along the bar length. They can be easily replaced and cover a working range related to the loader capacity.
The deactivation and activation of the device is automatically operated when the pusher passes through
The gripper unit allows the extraction and removal of the unusable bar remnant from the back side. The unit then introduces the new bar into the bar pusher collet. The gripper jaws are hydraulically operated and close in combination with an axial movement. They are designed to work at high operating pressure.
The rear remnant ejection has many advantages when compared to front ejection. For example, it avoids the risk of damage to the tools of the lathe and the components present in the tank. Furthermore it avoids possible obstruction of the swart conveyor .
The loading rack has an extension of between 600/1000 mm and it is designed in accordance with the lathe devices.
The selection of the single bar from the inclined plane is realised with a single adjustment, simplifying the process and reducing set up time.
This device is available only on the MULTls model.
The insertion of the Pusher release between the pushing section and the pusher extension confers on the unit the same solidity as the single pusher solution.
Moving the pusher from the loading channel axis allows the area usually occupied by the pusher itself to be used to receive the new bar. This solution allows a reduction of circa 1 min total length when compared to the MULTI model.